Tools Management System / TMS
The Tool Management System (TMS) is a powerful solution for efficiently managing tools, equipment, and consumables in the Maintenance Department. Designed to streamline operations, it offers centralized catalog management, precise tool tracking, inspection and calibration oversight, and an easy borrowing and retrieval system. With features like spare parts management, audit trails, superior approvals, and detailed inventory reports, TMS enhances productivity, accuracy, and control, catering specifically to production-focused needs.
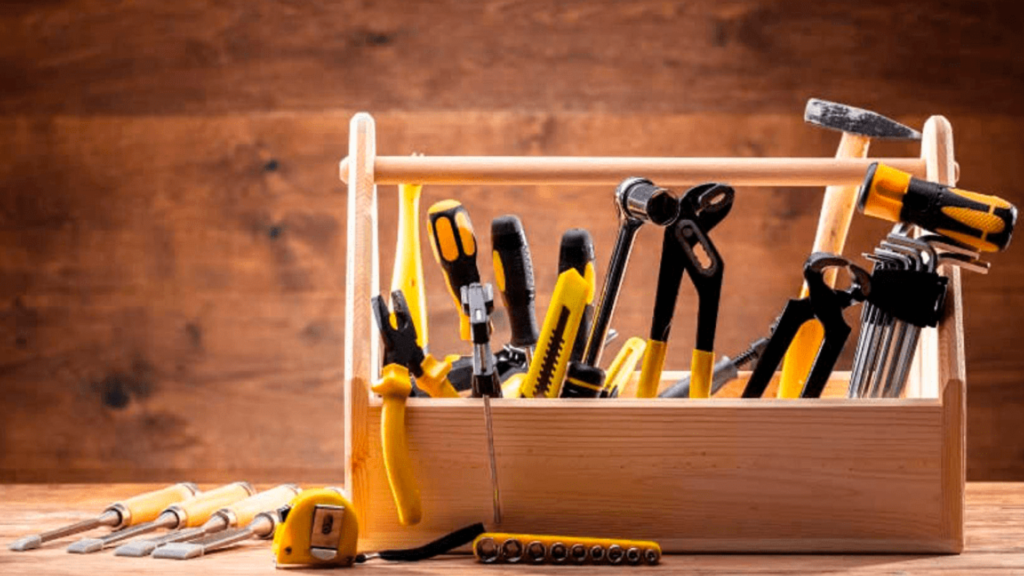
Introduction
Uniform Information Organization
1. Efficiently organizes and integrates plant tools information for streamlined operations.
Tool Catalog Management
2. Stores and manages the complete tool catalog in a centralized database via the tool management system.
Production-Specific Focus
3. Tailored to focus on production-specific data, distinct from broader management systems.
Spare Parts Management.
4. Handles spare parts used in production, ensuring proper tracking and data management.
Features
- Item identification and classification
- Tool tracking, manage and distribution
- Management of inspection and calibration
- Borrowing & retrieving system
- New Item requisition
- Audit trails for key transactions
- Superior approvals
- Periodical inventory report